With parts in every third car produced
Zinkteknik in Bredaryd, one of Europe’s leading zinc foundries, is in full swing. They have doubled their production since 2016 and the existing 11,000 m² was simply no longer sufficient. It was time to expand.
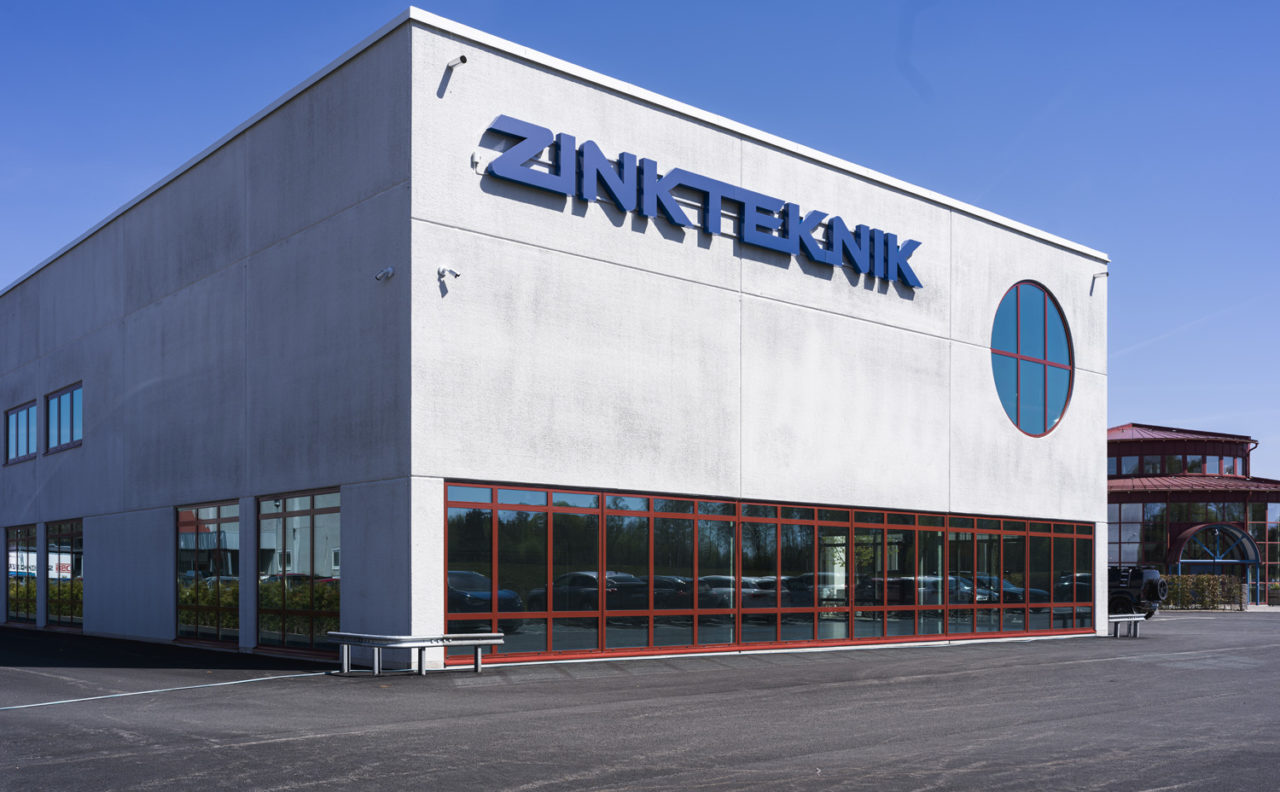
When you know that Zinkteknik’s parts are found in every third new car produced in the world today, you realise that the addition is welcome. They produce extremely high volumes every day and with a larger facility they can also optimise the flow through the plant – from raw material to finished part. Adding almost 50% to all departments is a major investment, but CEO and co-owner Niclas Svensson is confident in the decision.
– When we see the results, we can’t be anything other than proud and satisfied. Now we can grow with production and staff for many years to come. We are very happy with both the building and the execution, says Niclas happily.
– Zinkteknik and EAB are loyal partners. We have been working together since our first construction project in 1990 and in this project EAB has also delivered what was promised.
Niclas Svensson, CEO and co-owner, Zinkteknik
– Zinkteknik has been an exciting and extensive project! You could say that we have done it in three different parts, but within the same project. Part one was a minor extension of four piers in the existing premises, where we also added a fan housing on the roof,” states Jan Carlsson, project engineer at EAB Stålbyggnader.
EAB carried out a turnkey delivery with frame, roof, walls and trusses. We have also supplied all the concrete walls and concrete joists. Parts two and three of the construction were more extensive and included several customised solutions.
When the large extension, part two, was to be built, there was already a small production facility on site. The customer was very keen for production to continue as normal.
“The icing on the cake was when we installed EAB’s glazed doors, which improved natural light and improved aesthetics of the entire building.”
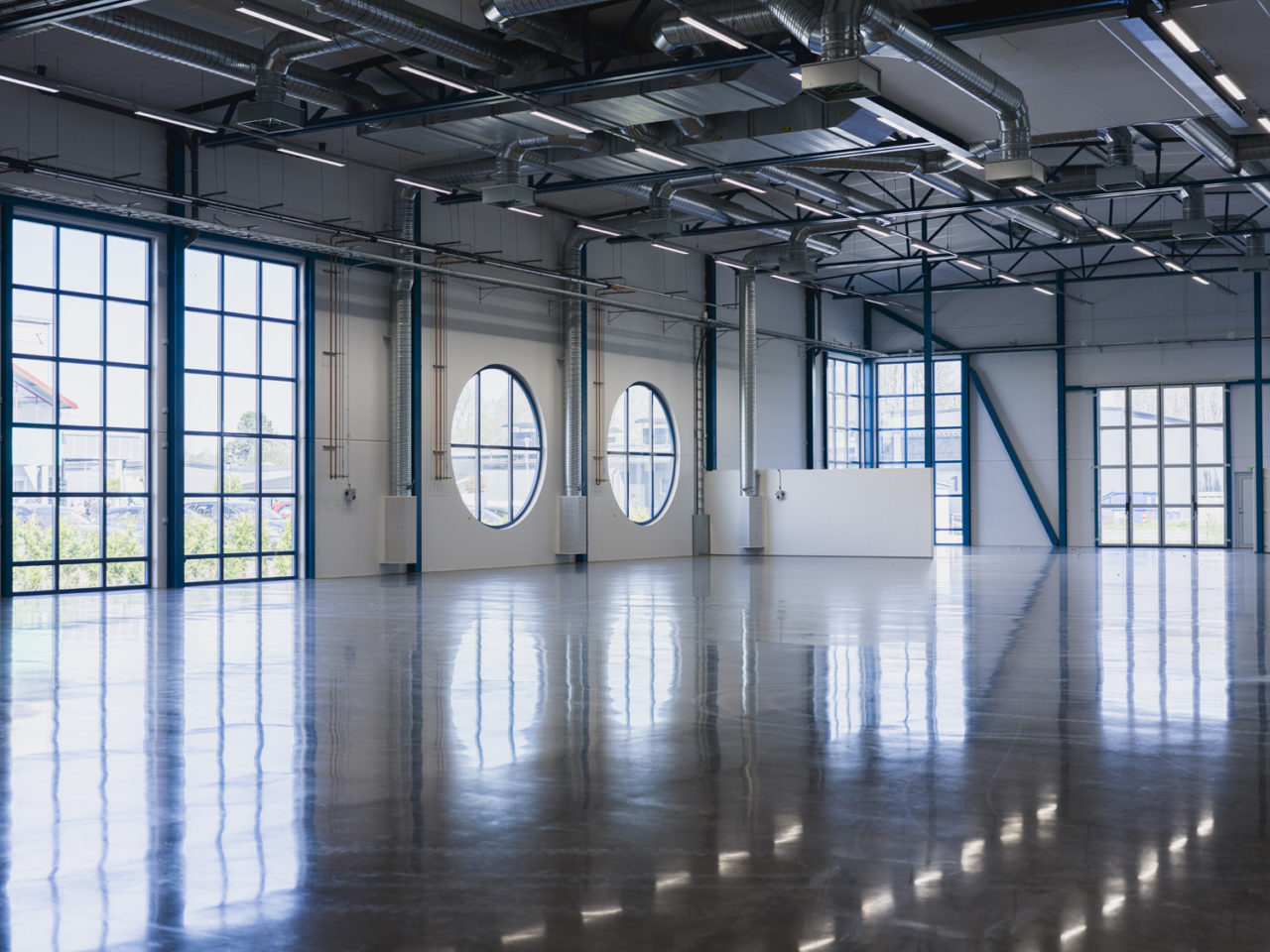
– Because all parts of the project have been completed around the existing premises, we were also able to reuse some of the wall elements. We kept the goal of having production up and running all the time,” says Jan, smiling.
– In the last two stages, we chose to raise the ceiling height by approximately two metres to create more space in our production halls. There was a clear difference in both satisfaction, light and acoustics that we have been praised for several times, both from both visitors and employees. The icing on the cake was when we installed EAB’s glass doors, which improved natural light and improved aesthetics of the entire building. Our operators often say that it feels like working outdoors, comments Niclas.
In addition to space to maximise production, Zinkteknik has also invested in new staff facilities. To accommodate an ever-growing staff group, the new facilities include a padel court, gym and sports hall. More changing rooms, a larger canteen, new offices and conference rooms were also a welcome addition and an important part of future growth