Beijer Byggmaterial invests
During an ongoing construction crisis, Beijer Byggmaterial is making the largest financial investment in the company’s history – a new central warehouse of 65,000 m² for the distribution of building materials. The new central warehouse is the size of twelve football pitches, has its own train tracks and state-of-the-art technology. This will contribute to faster and more sustainable deliveries while increasing the range for day-after delivery fivefold.
– This is a completely unique initiative and there is nothing like it in Sweden today. With the enormous capacity we get with the new central warehouse, we can give customers a completely new offer where, in addition to faster and more sustainable deliveries, they also get increased delivery security. This is because we are the ones who store the goods ourselves and can thus guarantee quality and that they are in place, says Henrik Ehrengren, Logistics Manager at Beijer Byggmaterial.
The central warehouse is located in Eskilstuna and will supply all of Beijer’s 116 stores with building materials and deliver directly to construction sites. The warehouse has a train track for transports straight into the property and a fully automated picking warehouse with about 100,000 places. It also has the environmental certification “Breeam Excellent”.
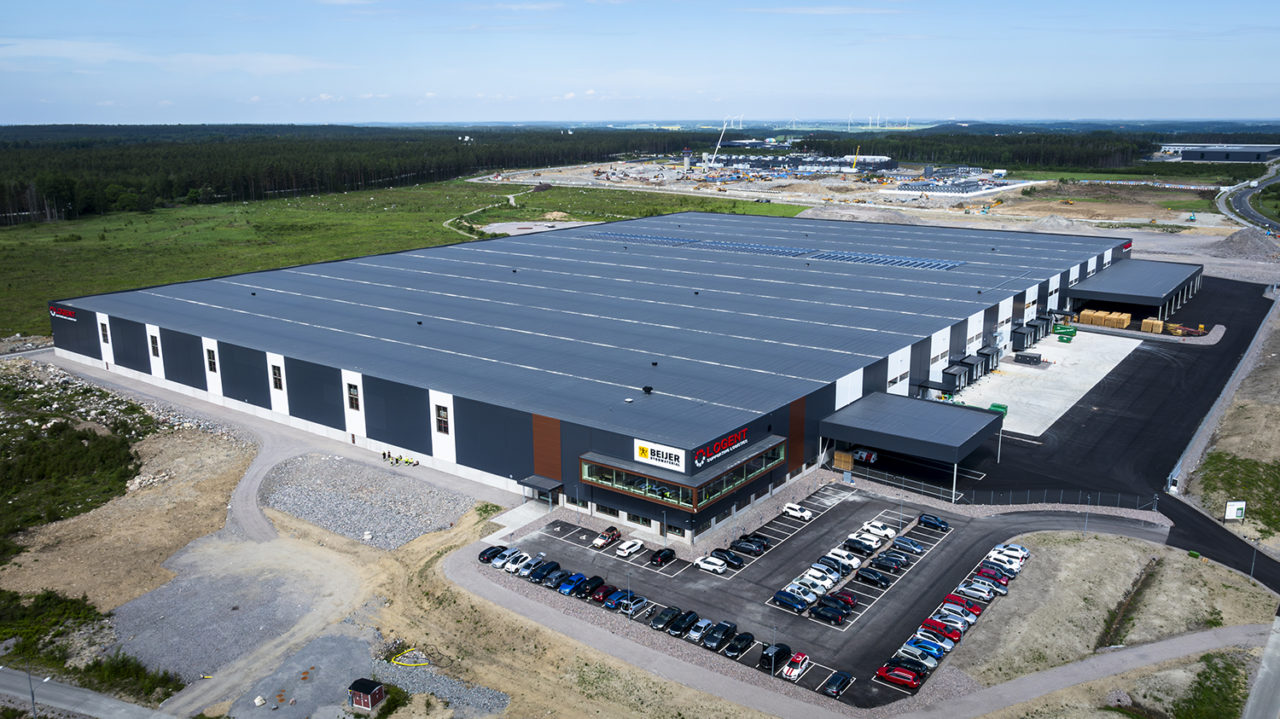
Efficient construction project
EAB has been involved in building the building, which was initially ordered by Charmilla Eskilstuna AB and which was acquired by Logicenters during the construction period.
– The project has had a good flow despite special adaptations. We have designed almost 10,000 square metres of canopies divided into four stages, where one of the canopies also includes a train quay, says Simon Davidsson, Project Engineer at EAB Steel Buildings.
We have delivered the frame, building envelope, 4,000 square metres of HDF floors, windows and doors. The assembly rate has been about 2,500 square metres per week, so it has gone very well, Simon adds.
“Our customers will get improved service through access to a significantly wider range for next-day delivery and also the ability to see the current balance in the central warehouse”
Henrik Ehrengren
Efficient and environmentally friendly solutions in focus
The warehouse has been built in close cooperation with logistics partner Logent, which is also responsible for the operation of the facility. Buster Odlander, project manager at Logent, describes the project as the most complex they have ever carried out.
– It’s a unique project with large volumes and variations of materials. Handling a smaller range and ordinary pallets is relatively easy, but here we have everything from small screws to 12 metre long beams. This has placed great demands on the warehouse equipment to cope with the entire span. The collaboration with EAB has been good and we are very satisfied with the products and functions of the warehouse equipment system, says Buster.
The property is environmentally certified, and the logistics solutions are designed to achieve maximum efficiency. Train tracks for transports straight into the property, fast charging for trucks during loading, electric forklifts in the warehouse and solar panels on the roof are some of the measures that have been implemented.
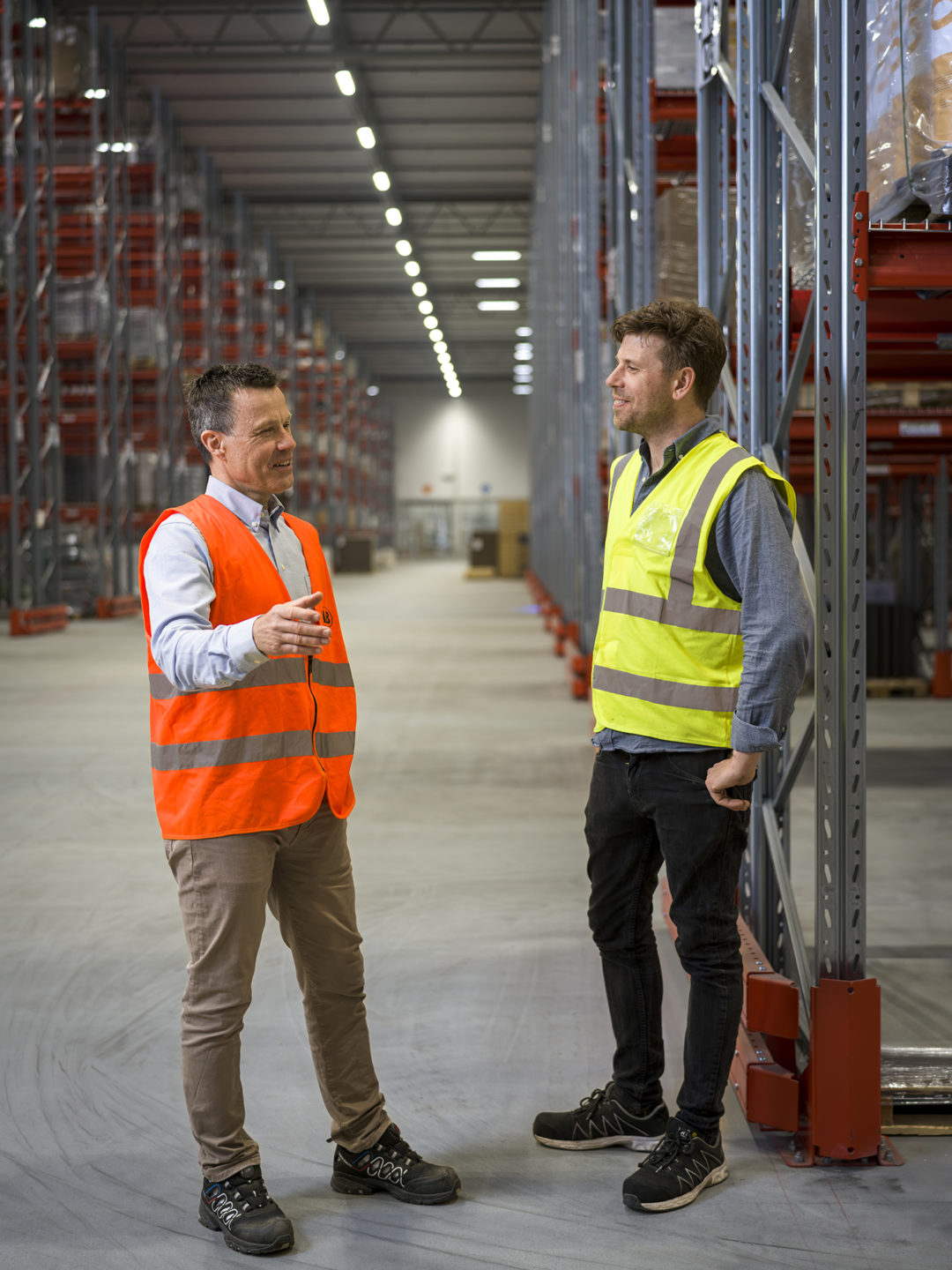
Positive cooperation
The construction of the central warehouse has been on schedule, which made it possible for the installation of the warehouse equipment to begin immediately after the New Year. The installation also went smoothly and already in mid-March the first goods could be loaded.
EAB has been an important partner in the project and Björn Jonsson, salesman and project manager at EAB Storage Equipment, thinks that the collaboration with Logent and Beijer Byggmaterial has been very good. The project has gone according to plan despite the short time for installation.
– We have supplied pallet racks, cantilever racks and list racks, which are our standard products. The challenge in the project has been the large volume of warehouse equipment and the complexity, says Björn.
The first deliveries from the new central warehouse took place in April and the business will gradually be expanded to reach full capacity in the autumn of 2024.
Buster has taken over as acting Site Manager for the past month and will thus continue to be part of the development of Beijer’s new central warehouse.
Increased demand for tailor-made logistics solutions
– In the future, customers want solutions that are adapted to their business and not pay for extra square meters that are empty. I think there will be more dedicated warehouse solutions and fewer based on pure speculation, Buster concludes.